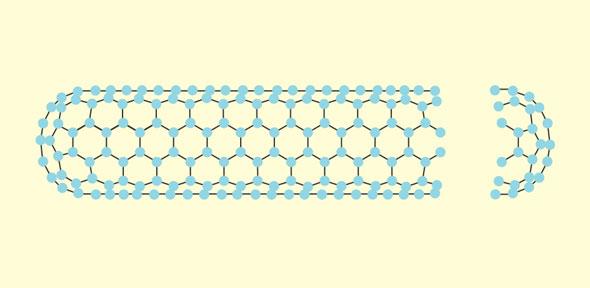
History’s deadliest swords – the ‘Damascene’ sabres forged in the Middle East from the 13th to the 18th centuries – were so sharp they could slice through falling silk, so legend has it. Their astonishing qualities are thought to have come from a combination of specific impurities in the iron ore and how hot and how long they were fired – a process that some scientists believe may have unwittingly created carbon nanotubes (CNTs) within them.
These thin, hollow tubes are only a single carbon atom in thickness. Like their carbon cousin, graphene – in which the atoms lie flat, in a two-dimensional sheet – they are among the strongest, most lightweight and flexible materials known.
“Fast-forward centuries,” said Dr Stephan Hofmann from the Department of Engineering, “and we now realise there is a whole family of these extraordinary origami forms of carbon… and how to make them.” In fact, the University has over 25 years’ cutting-edge experience in carbon nanotechnology, from diamond to nanotubes, and from conducting polymers to diamond-like carbon and graphene.
What makes carbon nanoforms such as graphene and CNTs so exciting is their electrical and thermal properties. Their potential use in applications such as lighter electrical wiring, thinner batteries, stronger building materials and flexible devices could have a transformational impact on the energy, transport and healthcare industries. As a result, investment totalling millions of pounds is now underpinning research and development in carbon-based research across the University.
“But all of the superlatives attributed to the materials refer to an individual, atomically perfect, nanotube or graphene flake,” Hofmann added. “The frequently pictured elephant supported by a graphene sheet epitomises the often non-realistic expectations. The challenge remains to achieve high quality on a large scale and at low cost, and to interface and integrate the materials in devices.”
These are the types of challenges that researchers in the Departments of Engineering, Materials Science and Metallurgy, Physics and Chemistry, and the Cambridge Graphene Centre have been working towards overcoming.
Professor Alan Windle from the Department of Materials Science and Metallurgy, for instance, has been using a chemical vapour deposition process to ‘spin’ very strong and tough fibres made entirely of CNTs. The nanotubes form smoke in the reactor but, because they are entangled and elastic, fibres can be wound continuously out of the reactor like nano candy floss. The yarn-like texture of the fibres gives them extraordinary toughness and resistance to cutting, making them promising alternatives to carbon fibres or high-performance polymer fibres like Kevlar, as well as for building tailored fibre-reinforced polymers used in aerospace and sports applications.
It is on the electrical front that they meet their greatest challenge, as Windle explained: “The process of manufacture is being scaled up through a Cambridge spin-out, Q-Flo; however, electrical conductivity is the next grand challenge for CNT fibres in the laboratory. To understand and develop the fibre as a replacement for copper conductors will be world-changing, with huge benefits.”
In 2013, Windle’s colleague Dr Krzysztof Koziol succeeded in making electric wiring made entirely from CNT fibres and developing an alloy that can solder carbon wires to metal, making it possible to incorporate CNT wires into conventional circuits. The team now makes wires ranging from a few micrometres to a few millimetres in diameter at a rate of up to 20 metres per minute – no small feat when you consider each CNT is ten thousand times narrower than a human hair.
With funding from the Royal Society and the European Research Council (ERC), the research is aimed at using CNTs to replace copper and aluminium in domestic electrical wiring, overhead power transmission lines and aircraft. CNTs carry more current, lose less energy in heat and do not require mineral extraction from the earth.
Moreover, they can be made from greenhouse gases; Koziol’s team is working with spin-out company FGV Cambridge Nanosystems to become the world’s first company to produce high-grade CNTs and graphene directly from natural gas or contaminated biogas. The company is already operating at an industrial scale, with high-purity graphene being produced at 1 kg per hour. “The aim is to produce high-quality materials that can be directly implemented into new devices, or used to improve other materials, like glass, metal or polymers,”
said Koziol.
Working directly with industry will be key to speeding up the transition from lab to factory for new materials. Hofmann is leading a large effort to develop the manufacturing and integrated processing technology for CNTs, graphene and related nanomaterials, with funding from the ERC and Engineering and Physical Sciences Research Council (EPSRC), and in collaboration with a network of industrial partners.
“The field is at a very exciting stage,” he said, “now, not only can we ‘see’ and resolve their intricate structures, but new characterisation techniques allow us to take real-time videos of how they assemble, atom by atom. We are beginning to understand what governs their growth and how they behave in industrially relevant environments. This allows us to better control their properties, alignment, location and interfaces with other materials, which is key to unlocking their commercial potential.”
For high-end applications in the electronics and photonics industry, achieving this level of control is not just desirable but a necessity. The ability to produce carbon controllably in its many structural forms widens the ‘materials portfolio’ that a modern engineer has at their disposal. With carbon films or structures already found in products such as hard drives, razor blades and lithium ion batteries, the industrial use of CNTs is becoming increasingly widespread, driven, for instance, by the demand for new technologies such as flexible devices and our need to harvest, convert and store energy more efficiently.
Professor Andrea Ferrari, Director of the Cambridge Graphene Centre and doctoral training programme, which has been funded through a £17 million grant from the EPSRC, explained: “People can now make graphene by the tonne – it’s not an issue. The challenge is to match the properties of the graphene you produce with the final application. Our facilities and equipment have been selected to promote alignment with industry; we have collaborations with over 20 companies who share our agenda of advancing real-life applications, and many more are discussing their involvement with our activities.”
Cambridge has pioneered graphene engineering and technology from the very start and, with multiple spin-offs, has become a hub for graphene manufacturing and innovation. The Cambridge Graphene Centre aims to improve manufacturing techniques for graphene and related materials, as well as explore applications in the areas of energy storage and harvesting devices, high-frequency electronics, photonics, flexible and wearable electronics, and composites. Graphene is also the focus of large-scale European funding – the Graphene Flagship, a pan-European 10-year, €1 billion science and technology programme was launched in 2013. Ferrari was one of the key investigators who prepared the proposal, has led the development of the science and technology roadmap for the project, and now chairs the Flagship’s Executive Board.
Now, building work has begun on a £12.9 million bespoke facility that will host the Cambridge Graphene Centre, with additional spaces for large-area electronics. The facility is due to open in late spring 2015.
“We recognise that there is still much to be done before the early promise becomes reality, but there are major opportunities now,” said Ferrari. “We are at the beginning of a journey. We do not know the final outcome, but the potential of graphene and related materials is such that it makes perfect sense to put a large effort into this early on.”
What links legendarily sharp Damascene swords of the past with flexible electronics and high-performance electrical wiring of the future? They all owe their remarkable properties to different structural forms of carbon.
The text in this work is licensed under a Creative Commons Licence. If you use this content on your site please link back to this page. For image rights, please see the credits associated with each individual image.