Clik here to view.
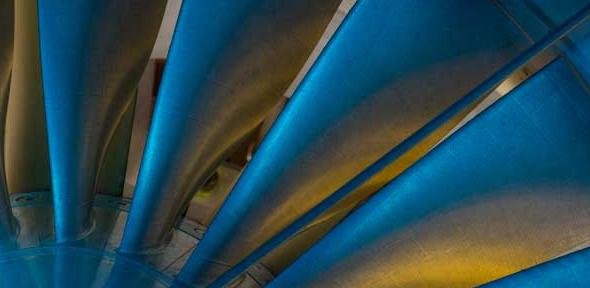
We’re seeing a transformational change in the propulsion and power sectors. Aviation and power generation have brought huge benefits – connecting people across the world and providing safe, reliable electricity to billions – but reducing their carbon emissions is now urgently needed.
Electrification is one way to decarbonise, certainly for small and medium-sized aircraft. In fact, more than 70 companies are planning a first flight of electric air vehicles by 2024. For large aircraft, no alternative to the jet engine currently exists, but radical new aircraft architectures, such as those developed by the Cambridge-MIT Silent Aircraft Initiative and the NASA N+3 project, show the possibility of reducing CO2 emissions by around 70%.
A common thread in these technologies and those needed for renewable power is their reliance on efficient, reliable turbomachinery – a technology that has been central to our work for the past 50 years. Currently we’re working on applications that include the development of electric and hybrid-electric aircraft, the generation of power from the tides and low-grade heat, like solar energy, and hydrogen-based engines.
We’re also working on existing technologies as a way of reducing the carbon emissions, like wind turbines, and developing the next generation of jet engines such as Rolls-Royce’s UltraFan engine, which will enable CO2 emission reductions of 25% by 2025. A great example is Dr Chez Hall’s research on a potential replacement for the 737. This futuristic aircraft architecture involves an electrical propulsion system being embedded in the aircraft fuselage, allowing up to 15% reduction in fuel burn.
A key element of meeting the decarbonisation challenge is to accelerate technology development. And so, over the past five years, our primary focus has been the process itself – we've been asking ‘can we develop technology faster and cheaper?’ The answer is yes – at least 10 times faster and 10 times cheaper. Our solution is to merge the digital and physical systems involved. In 2017, we undertook a pioneering trial of a new method of technology development. A team of academic researchers and industrial designers were embedded in the Whittle and given four technologies to develop.
The results were astonishing. In 2005, a similar trial took the Whittle two years. In 2017, the agile testing methods took less than a week, demonstrating a hundred times faster technology development.
We describe it as ‘tightening the circle’ between design, manufacture and testing. Design times for new technologies have been reduced from around a month to one or two days using augmented and machine-learning-based design systems. These make use of in-house flow simulation software that is accelerated by graphics cards developed for the computer gaming industry.
Manufacturing times for new technologies have been cut from two or three months to two or three days by directly linking the design systems to rows of in-house 3D printing and rapid machining tools, rather than relying on external suppliers. Designers can now try out new concepts in physical form very soon after an idea is conceived.
Testing times have been reduced from around two months to a few days by undertaking a ‘value stream analysis’ of the experimental process. Each sequential operation was analysed, enabling us to remove over 95% of the tasks, producing a much leaner process of assembly and disassembly. Test results are automatically fed back to the augmented design system, allowing it to learn from both the digital and the physical data.
There’s a natural human timescale of about a week whereby if you go from idea to result then you have a virtuous circle between understanding and inspiration. We’ve found that when the technology development timescale approaches the human timescale – as it does in our leaner process – then innovation explodes.
The New Whittle Laboratory will house the National Centre for Propulsion and Power, due to open in 2022 with funding from the Aerospace Technology Institute. A national asset, the Centre is designed to combine a scaled-up version of the agile test capability with state-of-the-art manufacturing capability to cover around 80% of the UK’s future aerodynamic technology needs.
Key to the success of the Whittle Laboratory has been its strong industrial partnerships – with Rolls-Royce, Mitsubishi Heavy Industries and Siemens for over 50 years, and with Dyson for around five years. So another component of the new development will be a ‘Propulsion and Power Challenge Space’. Here, teams from across the University will co-locate with industry to develop the technologies necessary to decarbonise the propulsion and power sectors.
The length and depth of these partnerships have so many benefits. They’ve enabled technology strategy to be shared at the highest level, and new projects to be kicked off quickly, without the need for contract lawyers. Joint industry–academic technology transfer teams move seamlessly between industry and academia, ensuring that technologies are successfully transferred into product.
Most importantly, the partnerships provide a source of ‘real’ high-impact research projects. It’s these long-term industrial partnerships that have made the Whittle the world’s most academically successful propulsion and power research laboratory.
We are at a pivotal moment, in terms of both Cambridge’s history of leading technology development in propulsion and power, and humanity’s need to decarbonise these sectors. Just 50 years ago, at the opening of the original Whittle Laboratory, research and industry faced the challenge of making mass air travel a reality. Now the New Whittle Laboratory will enable us to lead the way in making it green.
A bold response to the world’s greatest challenge
The University of Cambridge is building on its existing research and launching an ambitious new environment and climate change initiative. Cambridge Zero is not just about developing greener technologies. It will harness the full power of the University’s research and policy expertise, developing solutions that work for our lives, our society and our biosphere.
Read more about our research linked with Sustainable Earth in the University's research magazine; download a pdf; view on Issuu.
A rapid way of turning ideas into new technologies in the aviation and power industries has been developed at Cambridge’s Whittle Laboratory. Here, Professor Rob Miller, Director of the Whittle, describes how researchers plan to scale the process to cover around 80% of the UK’s future aerodynamic technology needs.
Image may be NSFW.
Clik here to view.
The text in this work is licensed under a Creative Commons Attribution 4.0 International License. Images, including our videos, are Copyright ©University of Cambridge and licensors/contributors as identified. All rights reserved. We make our image and video content available in a number of ways – as here, on our main website under its Terms and conditions, and on a range of channels including social media that permit your use and sharing of our content under their respective Terms.